
If kingpin replacement is required, a replacement kingpin should be selected which is similar to the type removed, or if a different style, one which can be adequately braced. If any deficiencies are noted during kingpin inspection, replace the kingpin (see Figure 5).Ĩ. For these reasons, SAF-Holland warns against any weld repairs. Additionally, arc strikes or weld craters could develop a stress riser, leading to a fatigue failure. Weld repairs of any type will affect the strength and wear resistance of the kingpin.

Kingpins are made from quenched and tempered alloy steel.
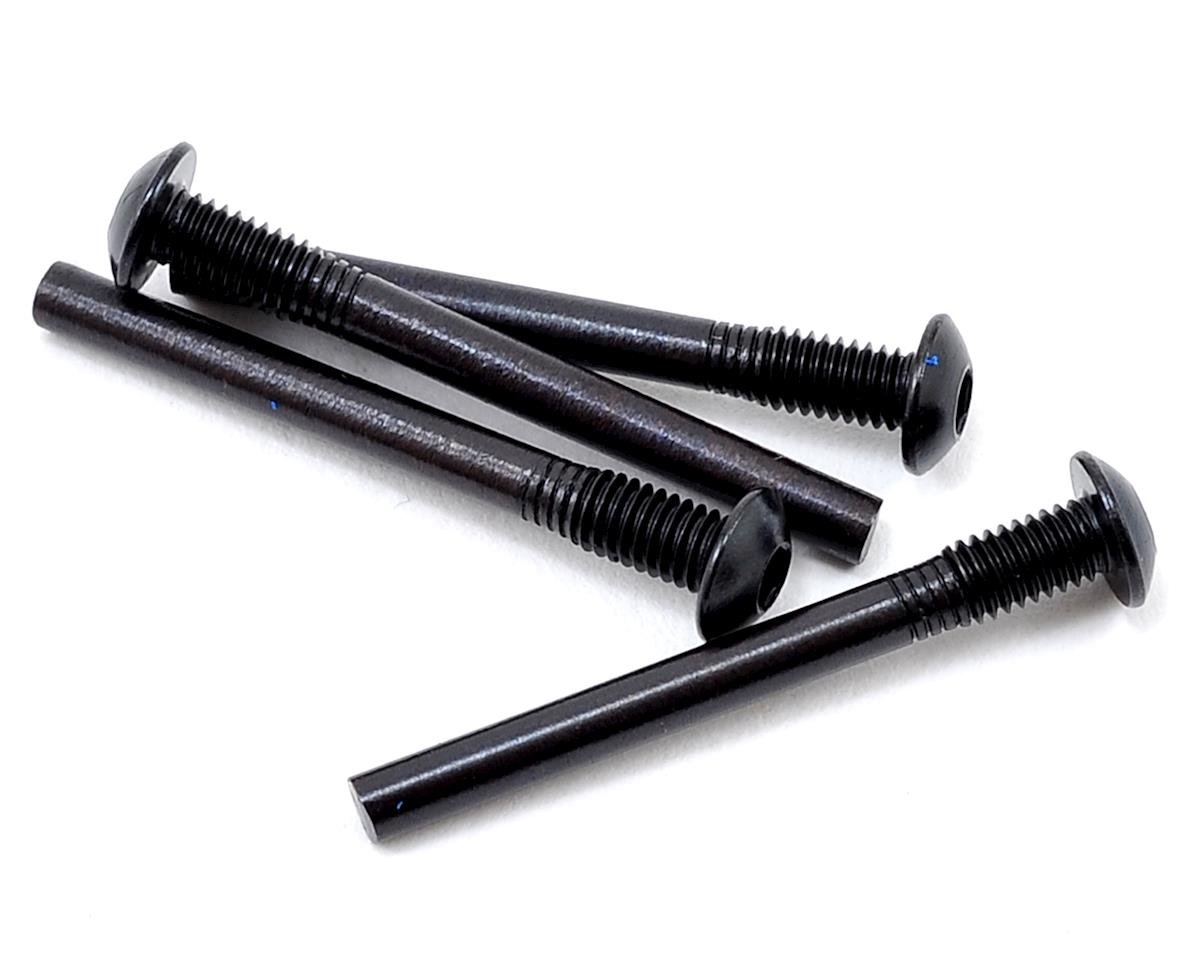
If any damage is present, replace the kingpin.ħ. Inspect the kingpin for any nicks, gouges, deformation, or cracks, which may interfere or affect the safe use of the kingpin. Reinstall or replace any kingpin that is not securely mounted.Ħ. A loose kingpin mounting will cause excessive chucking and rapid lock wear. Inspect the kingpin mounting for a secure connection to the upper coupler. If the gage slides into the gage slot, replace the kingpin.ĥ. If using a Holland Kingpin Gage, wear is indicated if the appropriate diameter enters the gage slot. If the kingpin is worn 1/8 inch (.125 inch) or more on either the 2-inch or 2-7/8-inch (2.875 inch) diameter in either direction, replace the kingpin. Check the kingpin for wear as shown in Figure 4. If the kingpin length is improper, the kingpin should be replaced.Ĥ. Otherwise, the kingpin will be too short. The kingpin must be sized to compensate for the thickness of the lube plate. If an add-on aftermarket lube plate is used in your operation, make sure to check the kingpin length. If either condition exists, replace the kingpin. A short kingpin will accelerate lock wear and may interfere with fifth wheel coupling. A long kingpin will result in excessive wear in the locks and coupling difficulty. Using a Holland Kingpin Gage, check the length of the kingpin for proper length as shown in Figure 3. The kingpin must be the proper length to couple properly with a fifth wheel.
